Several common silks in chemical fiber fabrics:
1. Filament: A continuous thin strip obtained by processing chemical fibers, which does not go through the cutting process is called filament. Filaments can be divided into the following categories according to their merging and twisting conditions:
Monofilament: A filament formed by a single-hole spinneret, usually a single continuous fiber of very long length.
Multifilament: A tow that consists of two or more monofilaments combined together.
Twisted yarn: It is made of multifilament twisted.
Composite twisted yarn: It is made by twisting the twisted yarn one or more times.
2. Textured yarn: A yarn formed by intertwining filament fibers without twisting is called textured yarn. Textured yarn can be divided into elastic yarn (low elastic yarn, high elastic yarn), air textured yarn, network yarn, etc. The textured yarn is the use of the thermoplasticity of synthetic fibers to thermally process or mechanically process ordinary synthetic filaments to make them have higher stretchability and bulkiness. The textured yarns produced by different texturing techniques have different fiber interlocking structures, so the yarn properties and styles are also different.
High elastic yarn or high elastic textured yarn has high bulkiness.
Low-stretch yarn or stretch-textured yarn (mainly polyester low-stretch yarn) is made of high-stretch yarn through heat setting, with moderate stretch and bulk.
Air-textured yarn is formed by the vortex cyclone of chemical fiber filament through the airflow nozzle to form a loop arc, so that the filament has the appearance of short fiber. The process of cutting chemical fiber filaments and spinning them into yarns is omitted in the production of air-textured yarns. Fabrics woven from air-textured silk have a look and feel close to those woven from staple fibers. Network filament refers to the filament in which the filaments are entangled with each other and form periodic network points through the action of jet air flow in the network nozzle.
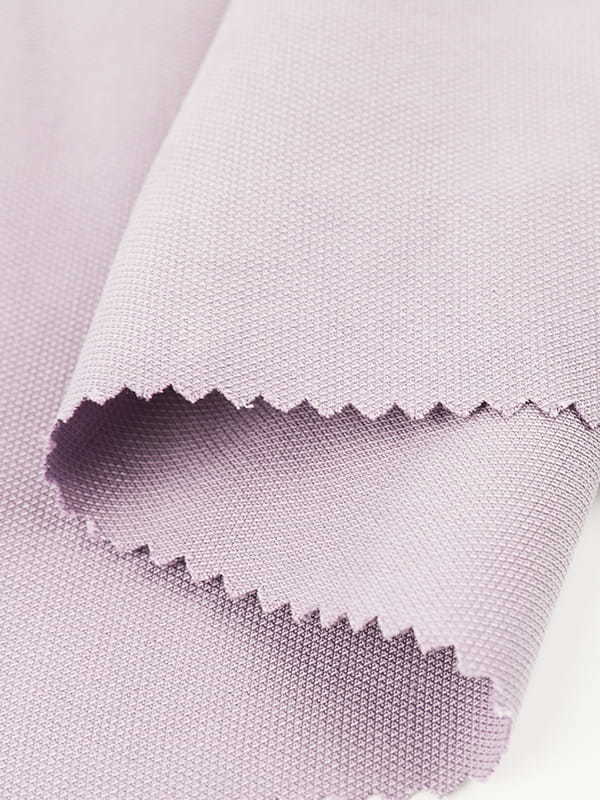
For short fibers, twisting is a necessary means of yarn formation; for filaments and strands, twisting is to form a compact structure that is not easily damaged by lateral external forces. The amount of twist, as well as the twist direction and twist coordination in the yarn and fabric, have a great impact on the fabric. By twisting the yarn, the cohesion between the fibers increases, the breaking strength and elongation at break increase, and the crepe resistance and wear resistance are enhanced; but the twist is too large, the stiffness of the fabric is too high, and the hem is easy to wear. and fracture. The twist direction has a great influence on the appearance of the fabric. When the yarn is untwisted, the optical fiber is reflected from each yarn, and the surface of the yarn is dark; the twist of the yarn is appropriate, the optical fiber is reflected from a relatively smooth surface, and the gloss is the strongest; if the twist is too large, the optical fiber is uneven on the surface of the yarn is absorbed between, and the reflected light is weakened as the twist increases.